When you’re thinking about how to join two pieces of metal together, you have two best options: welding or structural adhesive.
Welding and structural adhesive each have their own pros and cons, so it’s important to consider your goals when determining which method will work best for your specific situation.
Here are some of the key differences between welding and structural adhesive to help you determine which will be better in your case. And, you also shouldn’t skip panel bonding adhesive vs. welding.
What is Structural Adhesive?
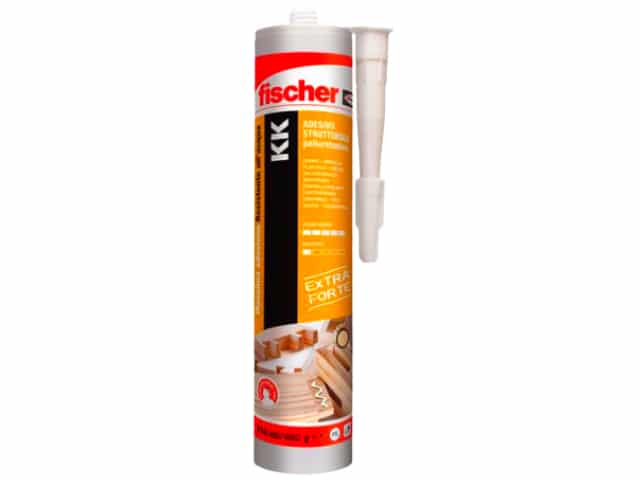
Structural adhesives are a popular construction product because they can do everything from repair concrete to help wood and steel bond together.
But why should you use them over traditional welding methods, such as TIG and MIG welding? In short, structural adhesives make it possible to create very strong bonds between similar and dissimilar surfaces in a way that doesn’t require toxic gases or additional heating elements.
What is Welding?
Welding is a process that is used to bond two pieces of metal together. It is available in a variety of formulations to suit different metals and applications.
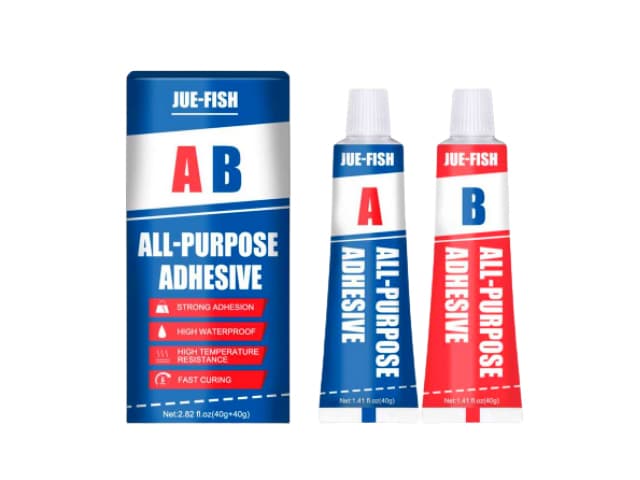
Welding is typically used in applications where a strong, permanent bond is required, such as in automotive and aerospace industries.
Read More: Contact Cement vs. Contact Adhesive
Structural Adhesive vs. Welding
Comparing Long-Term Performance
There are several key performance indicators to compare the long-term performance of structural adhesives and welding. Some of these indicators include:
-Tensile strength
-Elongation
-Tear resistance
-Shear strength
-Fatigue resistance
Generally, welding tend to perform better than structural adhesives in terms of these indicators. This is because welding are used specifically for bonding metals, while structural adhesives can be used on a variety of materials.
In terms of tensile strength, welding typically have a higher maximum load-bearing capacity than structural adhesives. For example, 3M’s Scotch-Weld Structural Adhesive Film AF 34-5490 has a tensile strength of 34 ksi, while its Scotch-Weld Welding EC-1261 has a tensile strength of 60 ksi.
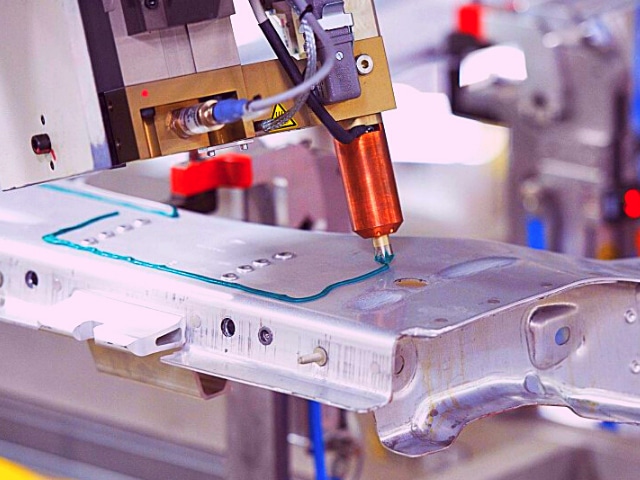
Elongation is another key indicator of adhesive performance. Welding tend to have higher elongation values than structural adhesives, meaning that they can stretch more before breaking. This is important for applications where the adhesive bond will be subject to stress or vibration.
Tear resistance is another important consideration for long-term performance. Welding typically have higher tear strength values than structural adhesives. This means that they are less likely to fail under conditions of stress or vibration.
Finally, fatigue resistance is a key indicator of long-term performance. Welding typically have better fatigue resistance than structural adhesives. This means that they are less likely to fail over time due to repeated stress or vibration.
Comparing Costs of Installation
There is no definitive answer to this question as it will depend on a number of factors, such as the type and size of the adhesive, the type of welding, the complexity of the project, and the experience of the installer.
However, in general, welding is usually more expensive than structural adhesive.
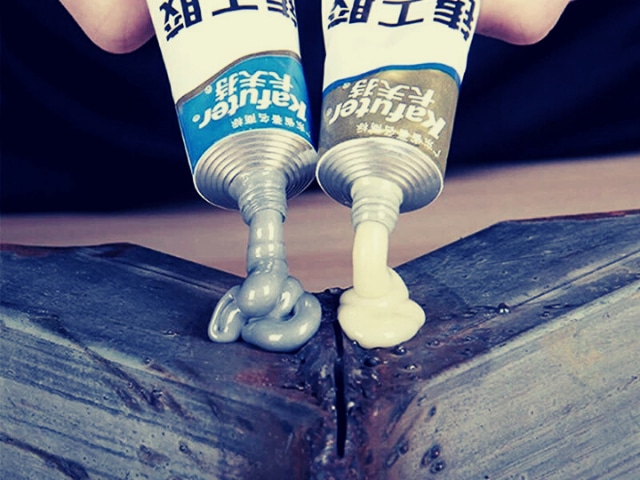
Comparing Ease of Installation
Both structural adhesive and welding can be installed easily. However, structural adhesives are great for easy, in-place installations and repairs, but if you’re a professional looking to install big projects quickly and with ease, welding will be a better choice.
What it comes down to is that structural adhesive has its limitations; while it can be useful as a backup or repair method, it simply can’t offer as much strength or durability as welding can.
Read More: JB Weld Strength vs. Welding
Listing Additional Benefits of Structural Adhesive
Structural adhesives offer a wide range of benefits because they are specifically designed to provide high-strength bonds.
Some of the main benefits of using structural adhesives include:
1. Increased Strength – Structural adhesives offer significantly higher bond strengths than traditional mechanical fasteners like screws or nails. This means that you can use smaller and lighter adhesives to achieve the same level of strength as heavier fasteners.
2. Increased Durability – Structural adhesives also offer increased durability compared to traditional fasteners. This means that your bonds will last longer and withstand more wear and tear.
3. Greater Flexibility – Structural adhesives offer greater flexibility than traditional fasteners, which means they can be used in a wider range of applications.
4. Greater Versatility – Structural adhesives can be used on a variety of different materials, including metals, plastics, glass, and wood. This makes them ideal for use in a wide range of applications.
5. Improved Aesthetics – Because structural adhesives create strong, seamless bonds, they can improve the aesthetics of your project.
6. Reduced Assembly Time – Structural adhesives can significantly reduce assembly time compared to traditional fasteners. This means you can complete your project faster and get it to market quicker.
7. Increased Efficiency – Structural adhesives can improve the efficiency of your production process by eliminating the need for secondary operations like drilling or tapping.
8. Reduced Waste – Structural adhesives can help reduce waste by eliminating the need for traditional fasteners and their associated packaging.
9. Cost Savings – Structural adhesives can offer significant cost savings compared to traditional fasteners. This is due to the increased efficiency and decreased waste that they offer.
10. Environmental Benefits – Structural adhesives can offer environmental benefits by eliminating the need for traditional fasteners and their associated packaging.
Last Opinion
Structural adhesive or welding can be used to install piping and conduit systems.
In most cases, structural adhesive can make your job easier, but not necessarily better—it depends on what kind of project you’re working on, as well as several other factors such as time constraints and budget.
You should always give careful consideration to both options before making a decision on which one to use for your own particular project.